Fabricar 30 baños a la semana o 1.000 metros de fachada al día: acelerar la construcción de viviendas desde la industria
La modernización del sector pasa por trasladar parte de los trabajos de las obras a las fábricas.
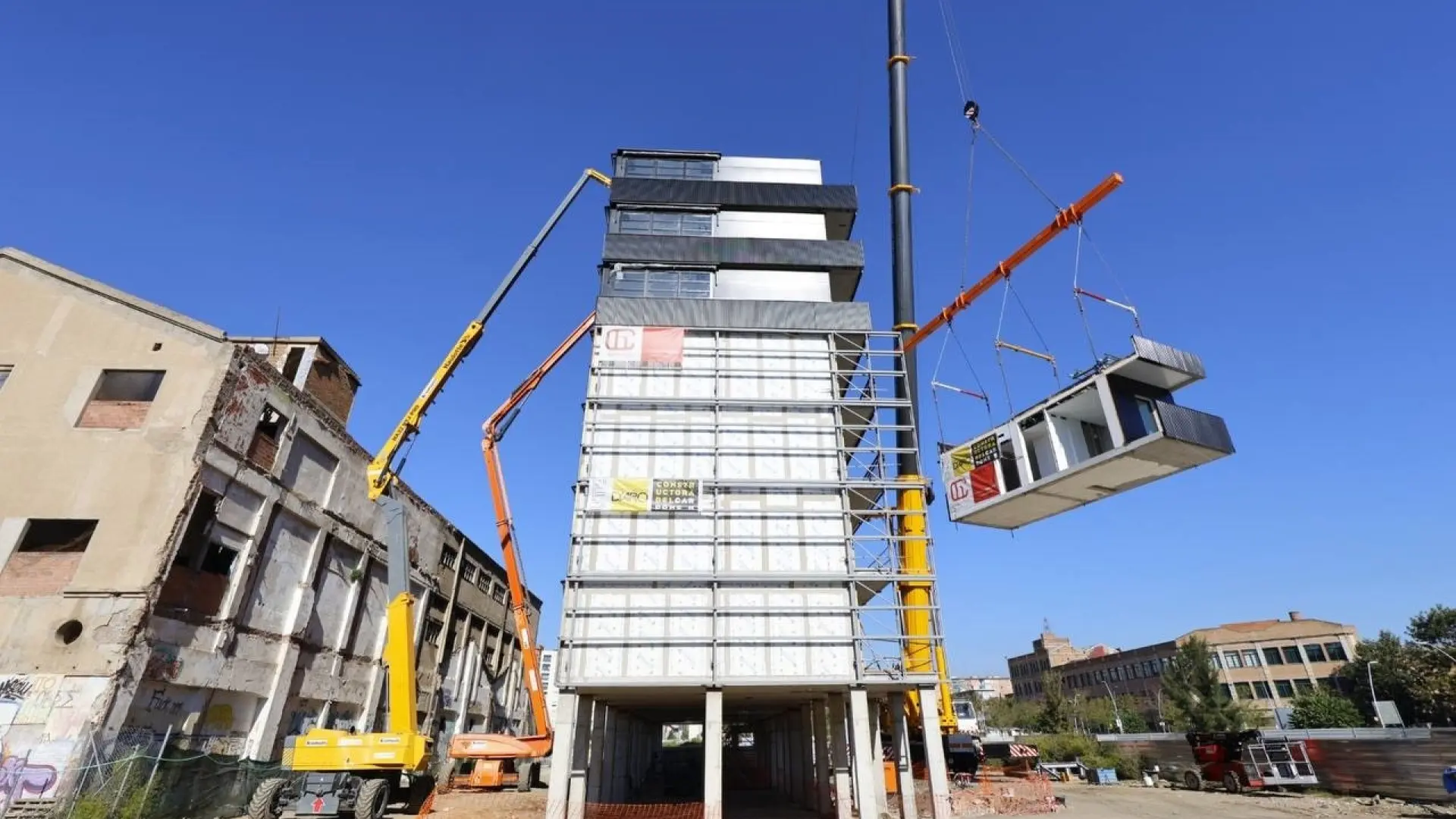
España acumula un déficit de 600.000 viviendas para cubrir la demanda de techo de los nuevos hogares, según cálculos del Banco de España. La escasez de pisos lleva tiempo empujando al alza los precios y la solución prácticamente de consenso pasa por construir más. Pero el problema es acuciante y los plazos de las obras, alargados. Para acelerar el ritmo, la última baza del Gobierno es apostar por la construcción industrializada, un modelo que consiste en la creación de componentes en fábrica que luego trasladar a la obra para ahorrar tiempo. Este cambio respecto al sistema tradicional supone apoyarse en la industria para impulsar la construcción, lo que requiere un tejido fabril más allá de las obras.
Según los datos manejados por el Gobierno, la construcción industrializada se emplea actualmente en apenas un 5% de los inmuebles levantados en España. Las primeras experiencias se han producido sobre todo en viviendas unifamiliares, aunque esta tecnología ya empieza a calar también en bloques de pisos, donde ahora se quiere potenciar. Fachadas y módulos de baños preelaborados en fábricas son los componentes que más presencia tienen en este tipo de promociones, pero el proceso para la aplicación de este método empieza antes incluso de que las máquinas empiecen a funcionar.
"La industrialización es posible si ya en fase de proyecto se piensa de forma industrializada. En la construcción tradicional los márgenes son de centímetros, pero en industrializada hablamos de milímetros. Si no hay un proyecto perfectamente milimetrado, es difícil el encaje", explica Diego Freire, presidente de la Asociación Española de Construcción Industrializada (AECI), que asegura que este sistema constructivo permite dar "certidumbre" a promotores y constructores y acortar tiempos.
"Es muy difícil hacer una promoción que no lleve sistemas industrializados y meterlos después", coincide Sandra Llorente, directora general de la empresa de soluciones industrializadas Lignum Tech, quien advierte de que desde el inicio de cada proyecto ha de tenerse en cuenta no solo qué componentes utilizar, sino también aspectos como su transporte, por ejemplo. "Es un proceso que va desde el concepto del diseño", recalca. "Una vez ya tienes todo estudiado, simplemente es comenzar la fabricación", señala la responsable de esta compañía de la corporación Vía Ágora, que desde su fábrica de Cuenca, y con la madera como principal materia prima, crea al año unos 88.000 metros cuadrados de fachada —el equivalente a unas 2.000 viviendas— y unos 25-30 módulos de baños a la semana.
Lo primero, junto a la provisión de materiales, es elaborar el prototipo que será reproducido para confeccionar el componente en cuestión. "Nosotros tenemos un desarrollo propio a través de inteligencia artificial donde metemos los distintos parámetros: cómo es el perímetro, cómo son los huecos, dónde está la estructura, las dimensiones del acabado final... Es un trabajo en el que antes tardábamos dos semanas completas y ahora en diez segundos sacamos las mejores propuestas", explica Llorente sobre el sistema empleado por la compañía para generar los prototipos de fachadas, el punto de partida de un proceso automatizado en el que las distintas máquinas de la cadena de producción se comunican entre sí para crear paneles que servirán de "piel" al edificio.
La clave para agilizar el proceso está en el uso de componentes estandarizados. "En vez de hacer un prototipo para cada obra, la tendencia actual es ir hacia un catálogo, lo que permite que el precio sea menor y hasta optimizar los materiales", explica Llorente. "Cuanto más estandarizados estén los sistemas constructivos industrializados, más competitivos serán y, por tanto, más atractivos para el promotor", coincide Freire, que apunta a que "hay que evitar que se improvise y se quiera industrializar a última hora un edificio previsto con producción tradicional o, por ejemplo, soluciones muy específicas, que acaban siendo labores más artesanales y es difícil que compitan en precio".
También la empresa Ávita se dedica desde 2022 a la confección de paneles para estructuras y fachadas desde su fábrica en Aranda de Duero (Burgos). Producen unos 600 al mes, el equivalente a unas 3.000 viviendas en un año. "Lo que nosotros proponemos no son solo los paneles, sino el sistema constructivo general que aplicamos en nuestras obras, basado el 90% en prefabricado", expone Miguel Ángel Argiz, director de la fábrica del Grupo Avintia, que apunta a que este funcionamiento les permite reducir los tiempos de ejecución de obra un 30%, llegando a poder tener terminada una vivienda en 16 meses frente a los dos años y medio que se suelen tardar habitualmente.
"Todo el proceso en fábrica empieza en un robot automatizado que coloca todos los encofrados y controla todas las posiciones que componen el carrusel. Sabe qué panel está fabricando, qué es lo que tiene que hacer y cómo va el proceso", explica Argiz, que subraya que todo el proceso de fabricación está automatizado, aunque con apoyo humano en cada fase. "El panel sale totalmente terminado de fábrica. Si lleva ventanas, puertas de acceso... todo sale montado y es simplemente colocarlo en obra", añade. Con estos componentes se nutren las obras del Grupo Avintia, que ya acumula 1.800 viviendas con elementos industrializados terminadas. "La demanda es cada vez mayor", reconoce Argiz, que explica que utilizan como materia prima el hormigón para crear "construcciones sólidas con una enorme durabilidad y resistencia".
Hormigón, madera, acero... son los materiales más usuales en los componentes industrializados, pero tampoco están reñidos con otro tan tradicional como el ladrillo. La Paloma Cerámicas, por ejemplo, fabrica al día desde Toledo en torno a 1.000 metros cuadrados de paneles de ladrillo, algunos para exportar incluso fuera de España. "Los hacemos en fábrica y se lleva a la obra. La ejecución es mucho más rápida que ir ladrillo a ladrillo. Es aproximadamente el doble de rendimiento. Y una vez instalado, no se ve que es un panel", explica Julio Pascual, director general de la compañía.
Otro de los elementos industrializados que más se usan en viviendas plurifamiliares son módulos de baños prefabricados. Desde Porcelanosa, compañía que cuenta con una división dedicada a ello, explican que el proceso comienza con el diseño de los planos, a partir de los cuales se fabrican y ensamblan los distintos componentes: paredes, suelo, accesorios, instalaciones eléctricas, mobiliario… El módulo sale de la fábrica completamente equipado, incluyendo tuberías y grifería, de manera que, una vez trasladado a la obra e izado con ayuda de una grúa, solo hace falta conectarlo a la instalación de fontanería y electricidad del edificio.
Una inyección de 1.300 millones
Impulsar este tipo de sistemas industrializados es el objetivo del nuevo Perte aprobado por el Gobierno, un proyecto estratégico que prevé una inyección de 1.300 millones de euros —fundamentalmente a través de préstamos del ICO— durante diez años para aumentar la capacidad productiva del tejido empresarial española hasta construir una media de 15.000 al año con componentes industrializados.
"Hay una industria naciente, pero hay que alimentarla para que vaya creciendo y se vaya estandarizando. Para eso, lo primero que se necesita es una demanda estable", plantea Freire, que ve en el plan gubernamental "un inicio, una muy buena noticia", aunque reclama, además, que las administraciones exijan un grado de industrialización en los proyectos públicos y que se regule el sector para aclarar qué considerar industrializado, en qué grado o cómo acceder a financiación. Por el momento, la ministra de Vivienda, Isabel Rodríguez, ya ha anunciado que en las próximas licitaciones de la Empresa Pública de Vivienda los elementos de industrialización puntuarán hasta un 10%.
"El Perte es una herramienta más. Todo suma. En definitiva es apoyo de las administraciones y una apuesta por este tipo de construcción", valora Argiz. También Llorente coincide en destacar el espaldarazo, aunque pide, asimismo, impulsar una formación especializada para dotar al sector de mano de obra y agilizar la burocracia en ayudas, permisos y obtención de certificaciones técnicas. Por su parte, Pascual llama a aprovechar la oportunidad para fomentar la innovación y la colaboración entre distintos fabricantes.