Wie Audi in seinem Stammwerk Ingolstadt Elektroautos produziert
Audis Stammsitz in Ingolstadt hat als erstes Werk eine eigene Batteriemontage. Wichtig war dem Hersteller die Integration von E-Autos in bestehende Strukturen. Der Beitrag Wie Audi in seinem Stammwerk Ingolstadt Elektroautos produziert erschien zuerst auf Elektroauto-News.net.
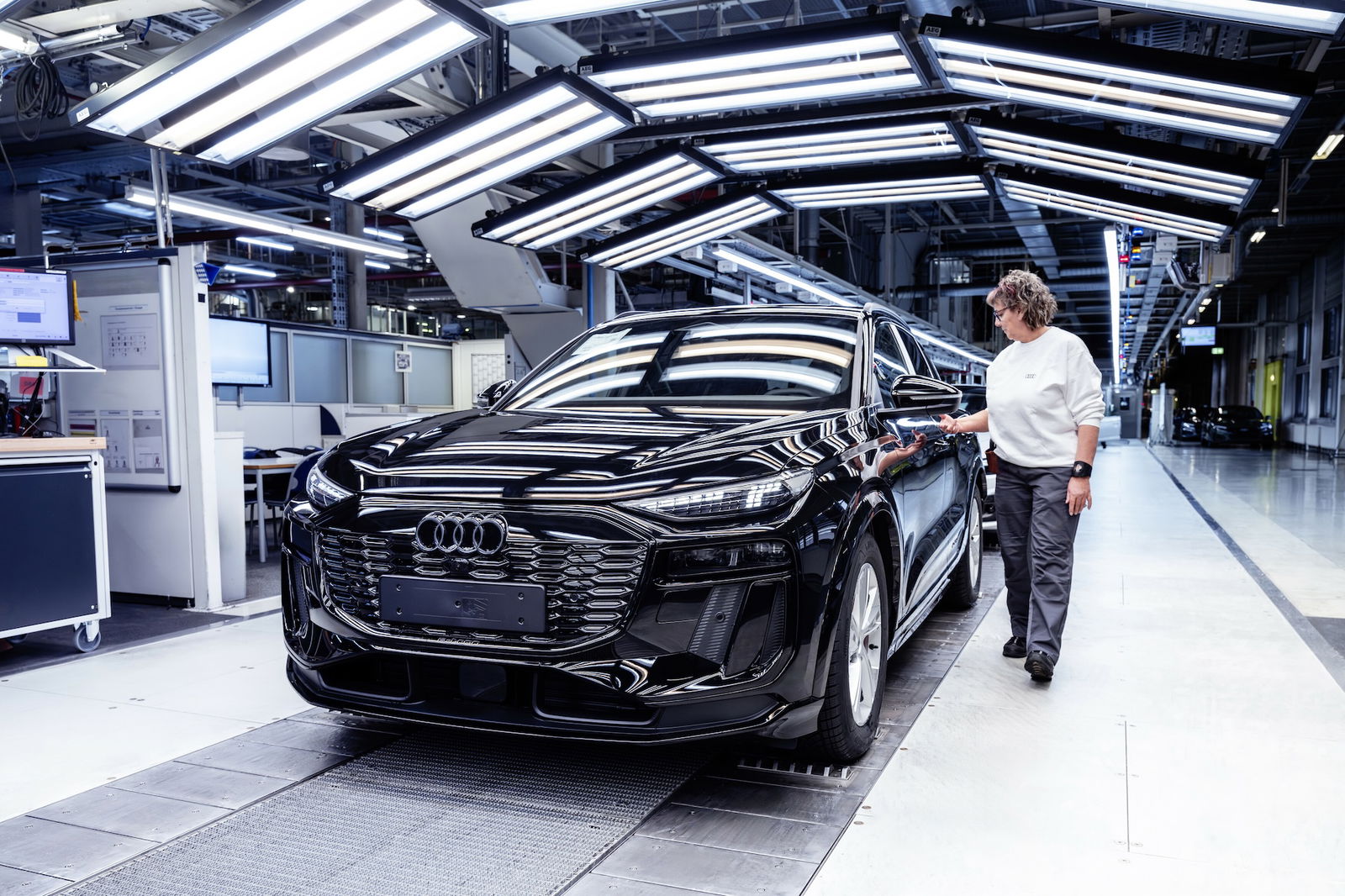
Die Audi Q6 e-tron Baureihe ist die erste vollelektrische Volumenbaureihe, die Audi im Stammwerk Ingolstadt produziert. Dabei setzt Audi gemäß der Produktionsstrategie 360factory im Karosseriebau und in der Montage auf eine Integration der einzelnen Produktionsschritte in bestehende Strukturen und Abläufe. Seit dem 1. Januar 2024 produziert Audi am Standort Ingolstadt außerdem bilanziell CO2-neutral. Zudem ist der Stammsitz der vier Ringe der erste deutsche Audi Standort mit einer eigenen Batteriemontage.
Audi CEO Gernot Döllner betont die Bedeutung des ersten Modells auf der neuen E-Auto-Architektur Premium Platform Electric (PPE), die gemeinsam mit Porsche entwickelt wurde. „Die PPE und damit die Q6 e-tron Baureihe ist die Basis für weitere elektrische Audi Modelle. Damit machen wir einen entscheidenden Schritt, um mittelfristig in allen Kernsegmenten ein E-Modell anbieten zu können.“
Audi Produktionsvorstand Gerd Walker ordnet den Produktionsstart Ende 2023 als wichtigen Meilenstein für die Produktionsstrategie 360factory ein: „Bis Ende des Jahrzehnts machen wir sukzessive alle Audi Standorte fit für Elektromobilität. Wir nutzen die Elektrifizierung für eine umfangreiche Transformation unserer bestehenden Werke. Mit der Produktion der Q6 e-tron Baureihe geht das Werk Ingolstadt den nächsten Schritt hin zur 360factory.“
Für die Fertigung der Zukunft hat Audi laut eigener Aussage eine klare Vision, verfolgt einen ganzheitlichen, nachhaltigen Ansatz und modernisiert, digitalisiert und transformiert seine bestehenden Werke. Ein Beispiel, wie Audi die Produktion modernisiert und in bestehenden Strukturen erweitert, ist die Batteriemontage für die Modelle auf Basis der PPE. Auf einer Fläche von rund 30.000 Quadratmetern montieren etwa 300 Mitarbeitende im Dreischichtbetrieb bei einer Automatisierungsrate von annähernd 90 Prozent täglich bis zu 1000 Hochvoltbatterien.
„Wir erhöhen damit nicht nur die Fertigungstiefe, sondern holen auch weitere Kompetenzen und Technologien direkt an den Standort“, sagt Produktionsvorstand Walker. Die Anlage in einer eigens für die Batteriemontage vorbereiteten Halle im Güterverkehrszentrum in Ingolstadt wird ausschließlich mit Ökostrom betrieben. Zudem erreicht Audi so eine höhere Flexibilität und Effizienz in der Fertigung, ohne für Neubauten weitere Flächen versiegeln zu müssen.
E-Motoren für PPE aus weltweit größtem Antriebswerk in Győr
Die E-Antriebe für die neue Technologieplattform Premium Platform Electric bezieht Ingolstadt aus dem laut Audi größten Motorenwerk der Welt im ungarischen Győr. Auf drei Linien fertigt Audi Hungaria dort E-Motoren für die PPE, die das Transportunternehmen DB Cargo CO2-neutral nach Ingolstadt liefert. Am Standort Győr fertigt Audi bereits seit 2020 bilanziell CO2-neutral. „Nachhaltig in bestehenden Werken zu fertigen, ist Kern unserer Produktionsstrategie 360factory und damit ein grundlegendes Element auf dem Weg zu einem zukunftsfähigen Produktionsnetzwerk“, sagt Walker.
Um die Q6 e-tron Baureihe nachhaltig und gleichzeitig effizient zu produzieren, hat Audi Produktionsbereiche wie den Karosseriebau für die PPE in bestehende Strukturen integriert. Auf einer Fläche von rund 148.000 Quadratmetern entstehen im Werk Ingolstadt die Karosserien für die PPE-Modelle. 328 Mitarbeitende je Schicht und 1150 Roboter fertigen bei einem Automatisierungsgrad von 87 Prozent die Karosseriebauteile für die Q6 e-tron Baureihe. Die flexible Plattformanlage ermögliche darüber hinaus den nahezu nahtlosen Anlauf von zukünftigen Modellen.
Um Ressourcen nachhaltig und synergetisch einzusetzen, verwendet Audi im Karosseriebau für die Fertigung der PPE-Karosserien mehr als 600 Maschinen wie Roboter wieder, die bereits in der Fertigung anderer Audi Modelle zum Einsatz gekommen waren. Für die Q6 e-tron Baureihe nimmt Audi zudem eine Flotte von mehr als 40 fahrerlosen Transportsystemen (FTS) neu in Betrieb. Die FTS übernehmen die Materialbereitstellung in der Halle und versorgen die Anlagen im Karosseriebau automatisiert mit notwendigen Teilen.
In der Montage nutzt Audi konsequent bestehende Strukturen und Anlagen. Die Q6 e-tron Baureihe integrierte der Hersteller in die ehemalige Montagelinie der Modelle A4 und A5. Audi integrierte die PPE-Modelle in die Montage in acht Umbauschritten.
Höherer Automatisierungsgrad in der Lackiererei
Auch die Lackiererei wurde für die neue vollelektrische Baureihe erweitert. Unter anderem wurde der Trockner nach dem Prozessschritt der KTL-Grundierung (Kathodische Tauchlackierung) verlängert und ein neues integriertes Verfahren zum automatischen Lochverschluss eingeführt. Dabei dichten Applikationsroboter nach der Grundierung rund 70 Löcher mit Klebepads an der zuvor für diesen Schritt vermessenen Karosserie ab. Ein Prozessschritt, der zuvor über Kopf von Mitarbeitenden manuell durchgeführt werden musste.
Um den höheren Energieaufwand für die Aushärtung der Karosserien nach der KTL zu gewährleisten, verlängerte Audi den Trockner. Auf diese Weise erreichen alle Karosserieteile die für die Aushärtung der KTL erforderliche Solltemperatur von 160 Grad Celsius. Zudem unterstützt in der Lackiererei in Ingolstadt eine automatisierte Fertigungstechnologie bei der Erkennung, Beurteilung und Abarbeitung von Oberflächenauffälligkeiten. Damit lässt sich die lackierte Oberfläche objektiv prüfen, die Prozesssicherheit erhöhen und das Qualitätsmonitoring transparenter durchführen.
Im ersten Schritt scannen Roboter mittels eines automatisierten Messsystems die Fahrzeugoberflächen. Dieses Verfahren bildet die Grundlage für das ebenfalls automatisierte Finish. Dafür ist jeder der Roboter mit einem Schleif- und Poliertool ausgestattet. Bei der anschließenden Kontrolle zeigen große Bildschirme den Mitarbeitenden die behobenen Stellen an.
Flexibles Anlagenkonzept bei der Warmumformung
Im Presswerk in Münchsmünster engagierten sich viele Fachleute intensiv, um auch den Prozess der Warmumformung für die PPE aufzuwerten. Durch dieses Verfahren werden vor allem sicherheitsrelevante Bauteile hergestellt. Denn Blechteile für die Karosseriestruktur der Fahrzeuge auf der PPE, wie A- und B-Säulen, sowie Teile des Längsträgers erhalten durch das Warmumformen eine besondere Stabilität und Crashsicherheit.
Nach dem Erhitzen in einer speziellen Ofenanlage auf rund 950 Grad Celsius werden Blechstreifen in einer Umformpresse mit zugehörigem Formwerkzeug zum Bauteil ausgeformt. Durch anschließendes lokales Abkühlen der erhitzten Blechstreifen mittels Luftdüsen beeinflusst Audi die Festigkeit der Bauteile gezielt, um das Crashverhalten zu optimieren und gleichzeitig das Gewicht der Karosserie zu verringern. Die besondere Härte des Materials macht es erforderlich, dass die Bauteile anschließend mithilfe von speziellen Lasern in die erforderlichen Konturen beschnitten werden.
Neben Bauteilen für Modelle auf Basis der PPE werden auch Bauteile für Modelle auf Basis der Verbrennerplattform PPC (Premium Platform Combustion) auf den Produktionsanlagen hergestellt. Durch die neu erreichte Flexibilität der Anlagen ist es möglich, insgesamt 44 verschiedene Bauteile in Münchsmünster herzustellen. Der Rüstwechsel an den Laserzellen und Umformpressen erfolgt vollautomatisch und in kürzester Zeit, so dass jeden Arbeitstag rund 20.000 Einzelteile das Werk verlassen können.
Quelle: Audi – Pressemitteilung vom 14.05.2025
Der Beitrag Wie Audi in seinem Stammwerk Ingolstadt Elektroautos produziert erschien zuerst auf Elektroauto-News.net.