Ultrasonic Thickness Gauge: A Comprehensive Guide for Accurate Material Inspection
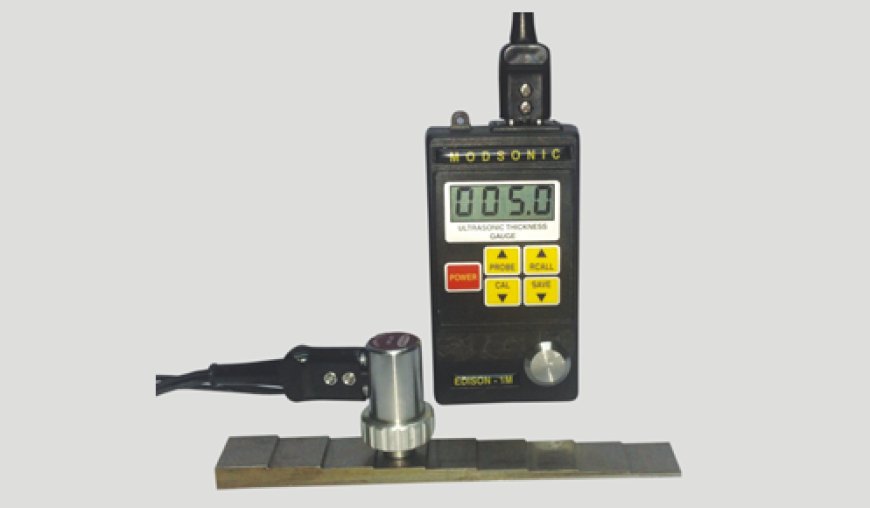
In various industries where safety, reliability, and quality are of paramount importance, monitoring the condition of materials is crucial. From pipelines to aircraft components and industrial equipment, material thickness plays a vital role in ensuring the strength, safety, and performance of the structure or device. One of the most effective methods for measuring material thickness is the ultrasonic thickness gauge.
Ultrasonic thickness gauges are an essential tool in non-destructive testing (NDT), allowing for precise measurement without causing any damage to the material being tested. Whether for detecting corrosion in pipelines, ensuring the quality of manufactured parts, or inspecting coatings on metal surfaces, ultrasonic thickness gauges are a versatile and reliable choice.
In this blog, we will delve into the workings of ultrasonic thickness gauges, their applications across industries, and the benefits they offer to ensure material integrity and operational efficiency.
What is an Ultrasonic Thickness Gauge?
An ultrasonic thickness gauge is a portable, non-destructive testing device used to measure the thickness of materials, such as metals, plastics, and composites, by sending high-frequency sound waves through the material. By measuring the time it takes for these sound waves to travel through the material and return, the device can calculate its thickness accurately.
The key feature of ultrasonic thickness gauges is that they do not damage the material being measured, making them ideal for routine inspections and ongoing monitoring. This non-destructive characteristic is especially important for critical infrastructure, where safety cannot be compromised.
How Does an Ultrasonic Thickness Gauge Work?
The principle behind ultrasonic thickness measurement involves ultrasonic waves, which are sound waves with frequencies higher than the human hearing range. These sound waves travel through the material being tested, and when they hit the back surface or boundary, they reflect back to the transducer. The time it takes for the waves to travel through the material and return is then measured and used to calculate the material’s thickness.
The process is fast, accurate, and provides reliable measurements with a minimal margin of error. Ultrasonic thickness gauges typically have a digital display that shows the thickness measurement in real-time, making them user-friendly and efficient for fieldwork.
Key Components of an Ultrasonic Thickness Gauge:
-
Transducer: The transducer is responsible for emitting and receiving the sound waves.
-
Couplant: A gel or liquid used to help transmit sound waves from the transducer into the material being measured.
-
Display Screen: A digital readout where the thickness measurement is shown.
-
Power Source: Ultrasonic thickness gauges are typically battery-operated, making them portable and easy to use in the field.
Types of Ultrasonic Thickness Gauges
There are several types of ultrasonic thickness gauges designed to meet the diverse needs of various industries. The main types include:
1. Handheld Ultrasonic Thickness Gauges
Handheld ultrasonic thickness gauges are compact, portable, and easy to use. They are ideal for quick, on-site inspections where immediate results are needed. These gauges typically provide a digital readout that shows the thickness measurement in real-time, making them perfect for routine maintenance and asset management. Handheld models are widely used in industries like construction, manufacturing, and maintenance.
2. Digital Ultrasonic Thickness Gauges
Digital ultrasonic thickness gauges offer additional features compared to handheld models. These gauges often come with data storage capabilities, allowing users to store and analyze measurement data over time. Digital gauges may also include additional functionality such as report generation, real-time graphing, and data logging. These advanced features make digital gauges suitable for industries that require detailed records, such as aerospace, oil and gas, and automotive manufacturing.
3. Dual-Element Ultrasonic Thickness Gauges
Dual-element ultrasonic thickness gauges have two elements in the transducer: one for sending and one for receiving the sound waves. This design improves measurement accuracy, especially for thicker materials or those with rough surfaces. Dual-element gauges are ideal for applications requiring high precision, such as pressure vessel inspections, aerospace component testing, and nuclear power plant inspections.
4. Coating Thickness Gauges
Coating thickness gauges are designed to measure the thickness of protective coatings on metal surfaces, such as paint, galvanization, or anti-corrosion coatings. These gauges typically use either ultrasonic or magnetic induction technology to measure the thickness of coatings. Coating thickness gauges are widely used in industries like automotive manufacturing, construction, and metal fabrication, where maintaining the integrity of coatings is critical for preventing corrosion.
Applications of Ultrasonic Thickness Gauges
Ultrasonic thickness gauges are used in a wide range of industries where material thickness and integrity are critical. Some of the most common applications include:
1. Oil and Gas Industry
In the oil and gas industry, pipelines and storage tanks are crucial for the transportation and storage of hazardous materials. These structures are often exposed to harsh environments that can lead to corrosion and thinning of the material. Ultrasonic thickness gauges are used to regularly monitor the thickness of pipelines and storage tanks, helping detect corrosion and wear before they lead to leaks, ruptures, or catastrophic failures. Regular testing ensures that the infrastructure remains safe and operational, reducing the risk of environmental damage.
2. Aerospace Industry
Aerospace components, such as aircraft wings, fuselages, and engine parts, are subject to high stresses and extreme environmental conditions. Ultrasonic thickness gauges are essential in the aerospace industry to monitor the condition of these critical parts. Regular inspections help detect signs of material fatigue, corrosion, or wear, ensuring that aircraft remain safe and reliable. Ultrasonic testing is especially important for ensuring that parts meet stringent performance and safety standards.
3. Manufacturing and Quality Control
In the manufacturing industry, ultrasonic thickness gauges are essential tools for quality control. They are used to monitor the thickness of materials during production, ensuring that parts meet specifications and safety standards. For example, ultrasonic gauges are used to measure the thickness of metal components in automotive manufacturing or to monitor the quality of welded joints. By detecting inconsistencies or defects early in the production process, ultrasonic gauges help improve the overall quality of the final product.
4. Shipbuilding and Marine Industry
In the maritime industry, ships and offshore structures are exposed to corrosive marine environments, which can accelerate material degradation. Ultrasonic thickness gauges are regularly used to inspect the thickness of hulls, decks, and other vital components of ships and offshore platforms. These inspections help detect corrosion or thinning areas, allowing for timely repairs that ensure the safety and longevity of marine vessels. Routine ultrasonic testing also helps prevent potential structural failures that could lead to accidents or environmental disasters.
5. Construction and Infrastructure
Ultrasonic thickness gauges are widely used in the construction industry to inspect structural components, such as steel reinforcements, beams, columns, and metal parts in buildings, bridges, and tunnels. These gauges help detect areas of material thinning or corrosion, ensuring that structures remain safe and sound over time. Ultrasonic testing is particularly useful for inspecting parts that are difficult to access or when conducting non-invasive inspections to avoid damage to the structure.
6. Automotive Industry
In the automotive industry, ultrasonic thickness gauges are used to measure the thickness of coatings such as rustproofing, paint, and galvanization applied to metal parts. These gauges ensure that coatings are applied correctly, providing adequate protection against corrosion and extending the lifespan of the vehicle. Ultrasonic thickness gauges are also used in quality control to ensure that metal components meet specifications and are free from defects.
Benefits of Using Ultrasonic Thickness Gauges
Ultrasonic thickness gauges offer numerous benefits that make them an invaluable tool for monitoring material integrity across various industries. Some of the key benefits include:
1. Non-Destructive Testing (NDT)
One of the primary advantages of ultrasonic thickness gauges is that they provide non-destructive testing. This means that the material being tested remains intact, and no damage is caused during the measurement process. As a result, ultrasonic thickness gauges can be used repeatedly without compromising the integrity of the material. This non-destructive feature is crucial for industries where materials need to be monitored regularly, such as in the oil and gas, aerospace, and manufacturing sectors.
2. High Accuracy and Precision
Ultrasonic thickness gauges are highly accurate and provide reliable, repeatable measurements. This precision is especially important when measuring materials that are exposed to high levels of stress, such as pressure vessels or aircraft components. By providing accurate readings, ultrasonic gauges allow technicians to detect even slight variations in material thickness, ensuring that potential issues are identified early.
3. Cost-Effective Maintenance
By detecting issues like corrosion, wear, or material thinning early, ultrasonic thickness gauges help companies perform targeted maintenance, preventing costly repairs or replacements. Early detection also helps reduce the risk of unplanned downtime, which can be expensive and disruptive. Regular use of ultrasonic thickness gauges can extend the lifespan of equipment and infrastructure, improving the return on investment (ROI) for companies.
4. Portability and Ease of Use
Ultrasonic thickness gauges are portable and easy to use, making them ideal for on-site inspections. Many models are lightweight and can be easily carried to remote or hard-to-reach locations. Their user-friendly design ensures that technicians can operate them with minimal training, making them an accessible tool for a wide range of applications.
5. Versatility
Ultrasonic thickness gauges can be used on a wide variety of materials, including metals, plastics, ceramics, and composites. This versatility makes them suitable for a broad spectrum of industries, from automotive manufacturing to construction and aerospace. Ultrasonic gauges are also capable of measuring a range of thicknesses, from very thin coatings to thick materials, which adds to their flexibility.
6. Improved Safety and Compliance
Using ultrasonic thickness gauges helps ensure that equipment and infrastructure meet safety standards and regulatory requirements. By identifying material degradation early, ultrasonic testing reduces the risk of accidents, failures, and safety hazards. Additionally, ultrasonic thickness gauges provide documentation that helps companies stay compliant with industry regulations and maintain certifications.
Conclusion
Ultrasonic thickness gauges are indispensable tools for industries where material integrity is critical to safety, performance, and cost-effectiveness. Their non-destructive nature, high accuracy, and versatility make them ideal for monitoring materials in various sectors, including oil and gas, aerospace, manufacturing, construction, and automotive industries.
By incorporating ultrasonic thickness gauges into regular maintenance and inspection routines, companies can detect issues early, reduce maintenance costs, and enhance safety. Whether it’s for monitoring corrosion in pipelines, ensuring the quality of coatings on automotive parts, or inspecting structural components in buildings, ultrasonic thickness gauges provide a reliable and cost-effective solution for ensuring material integrity. With their portability, ease of use, and precision, ultrasonic thickness gauges offer invaluable benefits to industries around the world, helping to maintain operational efficiency and prevent costly failures.