Wooden Pallet Manufacturers Leading Sustainable Supply Chain Solutions
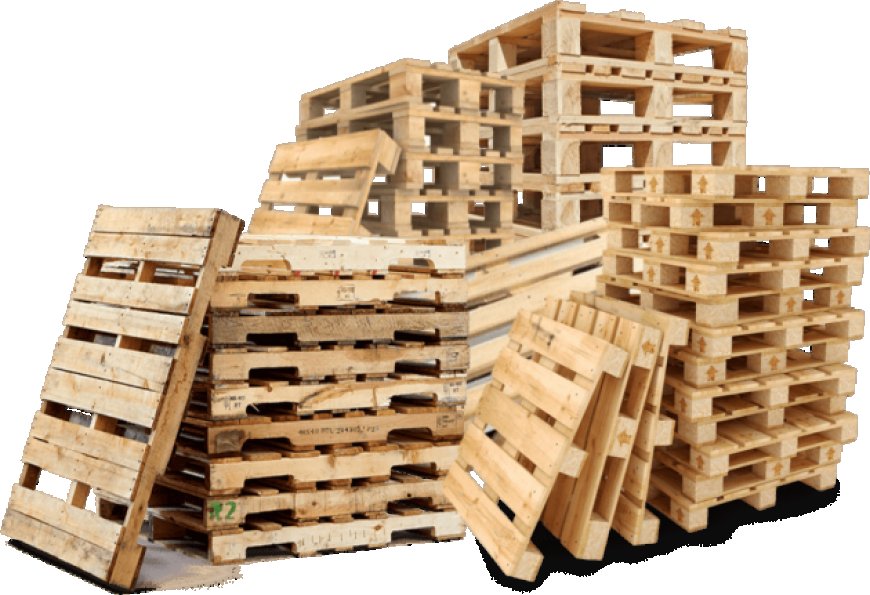
Wooden Pallet Manufacturers produce the essential platforms used globally for shipping and storing goods. They specialize in creating durable, standardized pallets that meet various industry specifications and handling requirements. The primary value they offer is reliable, cost-effective solutions tailored to the logistics needs of businesses.
These manufacturers source quality wood and use precise construction methods to ensure pallets withstand heavy loads and rough transportation conditions. Their expertise helps companies reduce damage and improve supply chain efficiency by providing consistent pallet designs.
Choosing the right wooden pallet manufacturer can impact operational costs and sustainability efforts. Understanding the options available, such as custom sizes or eco-friendly materials, helps businesses make informed decisions that support both performance and environmental goals.
Overview of Wooden Pallet Manufacturers
Wooden pallet manufacturers vary in size, technology, and product range. They focus on producing durable pallets that meet industry specifications and customer requirements. Manufacturing methods and quality controls differ, impacting the final product's reliability and certification status.
Key Industry Players
Leading manufacturers include companies like CHEP, Millwood Inc., and Conitex Sonoco. These firms supply pallets globally and emphasize sustainability and innovation. Smaller local manufacturers often cater to regional shipping needs with custom designs.
Some large manufacturers operate automated plants with high output, while others use semi-automated or manual systems. Market positions depend on production capacity, geographic reach, and adherence to environmental regulations.
Innovation and sustainability strategies, such as using recycled wood or heat treatment, distinguish key players. These manufacturers balance efficiency and compliance with international shipping standards.
Manufacturing Processes
The process starts with sourcing wood, often pine or hardwoods like oak. Wood is cut into standardized sizes, then dried to reduce moisture content before assembly. Nails or staples join the deck boards and stringers.
Many manufacturers employ automated nail guns and conveyor systems to improve speed and consistency. Others use manual methods for custom or smaller batches. Heat treatment or fumigation is applied to meet ISPM 15 regulations for international shipping.
Quality control checks for dimensions, weight capacity, and structural integrity at multiple stages. Waste wood is often recycled or repurposed to reduce environmental impact during manufacturing.
Common Wooden Pallet Types
Block pallets, stringer pallets, and double-face pallets are the most common types. Block pallets have blocks at the corners and center, offering four-way forklift entry. Stringer pallets use long boards (stringers) between the deck boards.
Double-face pallets have both top and bottom deck boards, increasing strength. Single-face pallets only have a top deck and require additional support for stacking. Custom pallets are also made for specific load requirements or transport conditions.
Dimensions typically follow standards like 48"x40" in North America or 1200x1000mm in Europe. Manufacturers often provide heat-treated or chemically treated options based on customer needs and regulations.
Quality Standards and Certifications
Manufacturers adhere to standards like ISPM 15 for phytosanitary treatment to prevent pest transfer. Certifications include heat treatment (HT), fumigation (MB), and kiln drying (KD), essential for international shipments.
ISO 9001 certification indicates quality management systems are in place. Some companies also follow sustainability certifications, such as FSC or PEFC, to prove responsible wood sourcing.
Regular inspections ensure pallets meet load-bearing capacity and durability requirements. Compliance with these standards minimizes shipping delays and enhances safety during transport and storage.
Selecting the Right Wooden Pallet Manufacturer
Choosing a wooden pallet manufacturer involves evaluating several key elements related to product quality, environmental impact, and service flexibility. Each decision factor directly affects cost efficiency, compliance with regulations, and overall supply chain performance.
Factors to Consider When Choosing a Supplier
Reliability and consistency in delivery schedules are critical factors when assessing pallet manufacturers. Companies should verify that the supplier maintains high production standards and uses quality wood to ensure pallet durability.
It is important to check the manufacturer's certifications, such as ISPM 15 for export pallets, to guarantee compliance with international shipping standards. Pricing transparency and volume discounts also play a role, especially for large or recurring orders.
Assess the supplier’s capacity to meet fluctuating demands and their customer support responsiveness. A manufacturer with a strong logistics network can reduce lead times and improve supply chain reliability.
Sustainability and Eco-Friendly Practices
Sustainability is increasingly significant when selecting a wooden pallet manufacturer. The use of responsibly sourced wood certified by organizations like the FSC (Forest Stewardship Council) reduces environmental impact.
Manufacturers that recycle wood waste or utilize biodegradable treatments align better with green procurement policies. Avoid suppliers relying heavily on chemical fumigation, as these might present environmental and safety concerns.
Certifications related to environmental management, like ISO 14001, signal a commitment to eco-friendly manufacturing processes. Buyers should consider manufacturers with programs for pallet reconditioning or take-back to extend pallet life cycles.
Customization and Value-Added Services
Manufacturers that offer tailored pallet designs improve operational efficiency by matching specific storage or transport needs. Custom sizes, load capacities, and branding options allow companies to optimize space and brand visibility.
Additional services such as pallet pooling, repair, and just-in-time delivery can mitigate inventory costs and minimize downtime. The availability of design consultation helps users select pallets best suited for their product types and logistics requirements.
Some manufacturers provide heat treatment or fumigation to meet export regulations. Verifying these service options is essential when dealing with international shipments or specialized cargo.