Optymalizacja produkcji – jak wygląda proces?
W dzisiejszym konkurencyjnym świecie biznesu firmy produkcyjne poszukują sposobów na zwiększenie swojej efektywności. Optymalizacja produkcji to proces, który sprawia, że zakłady działają sprawniej, taniej i z większą dbałością o jakość oraz środowisko. Nie chodzi tu o rewolucję, ale o mądre usprawnienia, z których korzystają wszyscy: producenci, klienci i planeta. Przyjrzyjmy się krok po kroku, jak wygląda ten proces. Mamy nadzieję, że po lekturze naszego przewodnika zagadnienie pt. optymalizacja produkcji - jak wygląda proces? stanie się o wiele łatwiejsze do zrozumienia.
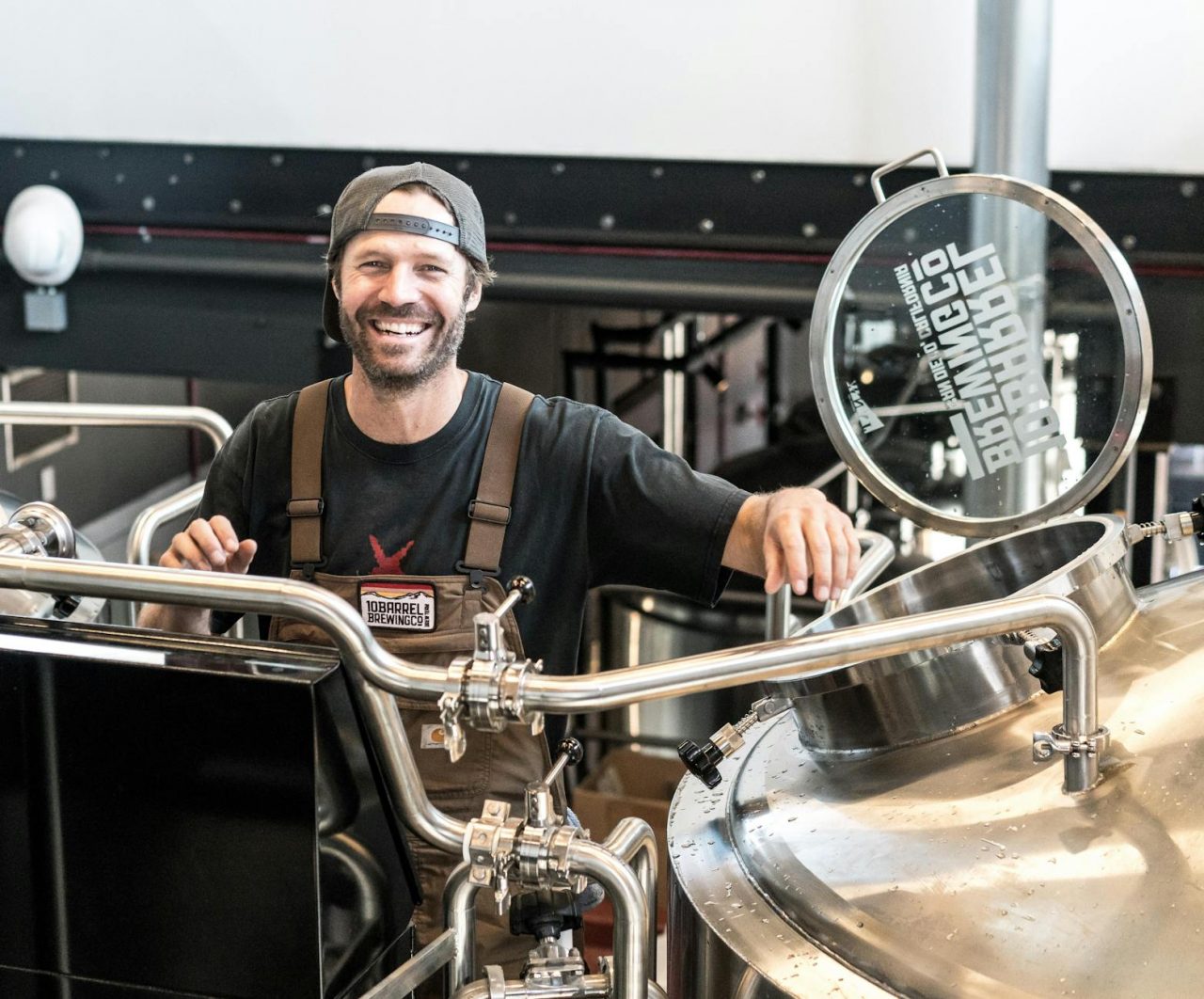
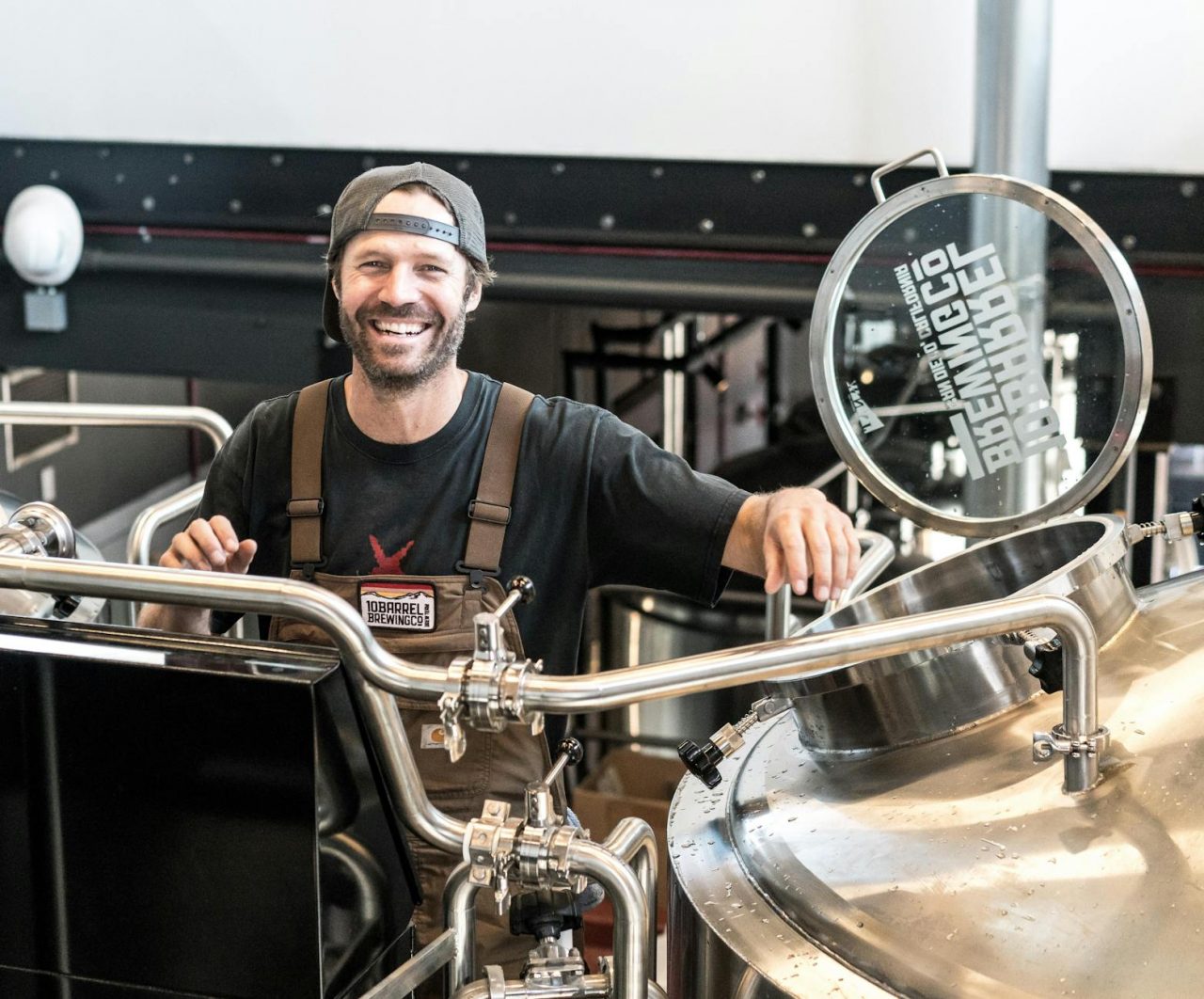
Czym jest i jaki jest cel optymalizacji produkcji?
Optymalizacja produkcji jak wygląda proces? To nic innego jak systematyczne usprawnianie wszystkich działań związanych z wytwarzaniem produktów. Jej głównym celem jest zwiększenia wydajności – osiąganie lepszych rezultatów przy wykorzystaniu tych samych lub mniejszych zasobów. Przekłada się to bezpośrednio na redukcję kosztów i poprawę jakości produktów.
Warto podkreślić, że korzyści z optymalizacji produkcji wykraczają poza samą firmę. Klienci otrzymują wyroby wyższej jakości, często szybciej i w lepszej cenie. Dodatkowo zyskuje również środowisko naturalne – zoptymalizowane procesy zazwyczaj oznaczają mniejsze zużycie energii, surowców i generują mniej odpadów produkcyjnych. To sytuacja, w której wszyscy wygrywają.
Analiza obecnego procesu produkcyjnego
Pierwszym krokiem w procesie optymalizacji jest dokładne zbadanie aktualnego stanu. Nie da się bowiem usprawnić czegoś, czego nie rozumiemy. Kluczowe jest tutaj mapowanie procesów – szczegółowe przyjrzenie się każdemu etapowi od momentu przyjęcia surowców, poprzez poszczególne operacje, aż do momentu, gdy gotowy produkt opuszcza fabrykę.
Podczas tej analizy identyfikuje się tzw. marnotrawstwo – wszystko, co nie dodaje wartości produktowi z punktu widzenia klienta. Może to być nadprodukcja (wytwarzanie większej ilości niż potrzeba), zbędny ruch, przestoje, defekty, nadmierne zapasy czy niepotrzebny transport. Identyfikacja obszarów generujących straty jest punktem wyjścia do zaplanowania konkretnych usprawnień. Interesuje Cię ten temat? Sprawdź szczegóły na stronie optymalizacja produkcji bez tajemnic.
Wdrażanie narzędzi i metod optymalizacyjnych
Gdy wiemy już, co wymaga poprawy, czas na działanie. Metody optymalizacji procesów często wywodzą się z japońskiej myśli przemysłowej i obejmują.
Lean Manufacturing – filozofia skupiona na minimalizację marnotrawstwa i tworzenie większej wartości przy mniejszym nakładzie zasobów.
Kaizen – koncepcja ciągłego doskonalenia poprzez wprowadzanie wielu małych zmian, angażując wszystkich pracowników.
Six Sigma – metoda mająca swoje korzenie w USA, skoncentrowana na redukcji błędów i defektów, dążąca do osiągnięcia niemal doskonałej jakości.
Oprócz tych metodyk wdraża się również konkretne narzędzia, takie jak standaryzacja pracy, systemy zarządzania zapasami (np. Just-in-Time), czy techniki rozwiązywania problemów. Celem jest uproszczenie procesów i zwiększenie ich płynności.
W których branżach optymalizacja produkcji może przynieść szczególne efekty?
Bardzo często przy okazji tematu optymalizacja produkcji – jak wygląda proces? Pojawia się wątek, gdzie przyniesie ona największe profity. Choć optymalizacja procesów jest korzystna niemal wszędzie, w niektórych sektorach jej wpływ jest szczególnie widoczny.
W przemyśle motoryzacyjnym – precyzyjna synchronizacja etapów, minimalizacja błędów i redukcja czasów cyklu przekładają się na ogromne oszczędności. To właśnie w Toyocie narodziła się filozofia Lean.
W branży elektronicznej, gdzie komponenty są małe, a połączenia skomplikowane, automatyzacja procesów i systemy monitoringu są kluczowe dla jakości i ograniczenia strat kosztownych materiałów.
Przemysł spożywczy wymaga sprawnego zarządzania surowcami o krótkiej trwałości, dlatego optymalizacja przepływu materiałów i skrócenie czasu realizacji zamówień ma tu ogromne znaczenie.
W farmaceutyce najwyższe standardy jakości, precyzja dawkowania i identyfikowalność każdej partii są krytyczne. Optymalizacja produkcji pozwala zwiększyć skalę przy zachowaniu rygorystycznych norm.
Przemysł chemiczny, często energochłonny, dzięki optymalizacji może znacząco wpłynąć na obniżenie kosztów produkcji oraz bezpieczeństwo pracowników i środowiska.
Automatyzacja i technologie cyfrowe
Współczesna optymalizacja produkcji w dużej mierze opiera się na zaawansowanych technologiach. Automatyzacja procesów produkcyjnych, czyli zastosowanie robotów i maszyn, przyspiesza procesy, zwiększa precyzję i powtarzalność, a także redukuje ryzyko błędów ludzkich.
Systemy informatyczne takie jak MES (Manufacturing Execution Systems) pozwalają na gromadzenie danych z produkcji w czasie rzeczywistym, monitorowanie statusu maszyn i zarządzanie procesami produkcyjnymi. Analiza danych umożliwia wyciąganie wniosków i identyfikowanie dalszych obszarów do poprawy. Technologie te integrują różne etapy produkcji i dostarczają menedżerom cenne informacje, umożliwiając szybsze i lepsze decyzje.
Monitorowanie i pomiar efektów
Wprowadzenie zmian to dopiero połowa sukcesu. Aby wiedzieć, czy idziemy w dobrym kierunku, niezbędne jest monitorowanie wydajności i mierzenie efektów. Służą do tego tzw. wskaźniki KPI (Key Performance Indicators), czyli kluczowe wskaźniki efektywności.
KPI w zakładach produkcyjnych mogą obejmować takie parametry jak: czas cyklu produkcyjnego, poziom defektów, wydajności maszyn, koszty jednostkowe, terminowość dostaw czy poziom zapasów. Regularna analiza danych o tych wskaźnikach pozwala na bieżącą ocenę skuteczności wprowadzonych zmian i szybkie reagowanie na pojawiające się problemy w ramach filozofii ciągłego doskonalenia procesów.
Zaangażowanie pracowników i kultura organizacyjna
Nawet najlepsze technologie i metody nie przyniosą trwałych efektów bez zaangażowania ludzi. To pracownicy na hali produkcyjnej często najlepiej znają codzienne problemy i mają najcenniejsze pomysły na usprawnienia.
Wdrożenie optymalizacji wymaga aktywnego udziału całego zespołu. Kluczowe jest stworzenie kultury organizacyjnej, która promuje transparentną komunikację, otwartość na zmiany i zachęca do zgłaszania pomysłów usprawnień. Szkolenie pracowników jest niezbędne, aby przygotować personel do pracy z nowymi narzędziami i metodami. Zaangażowany, świadomy zespół jest fundamentem skutecznej optymalizacji.
Optymalizacja to korzyści dla wszystkich stron
Proces optymalizacji przynosi wymierne korzyści dla wszystkich uczestników.
Dla producenta oznacza niższe koszty produkcji (mniej odpadów, mniejsze zużycie energii, wyższa wydajność maszyn), lepszą jakość wyrobów i zwiększenie elastyczności w reagowaniu na wymagania rynku.
Klienci otrzymują produkty wyższej jakości, często w lepszej cenie i z krótszym czasem oczekiwania na realizację zamówienia. Wzrasta również niezawodność dostaw.
Środowisko naturalne zyskuje dzięki lepszemu wykorzystaniu zasobów, ograniczeniu ilości generowanych odpadów i bardziej zrównoważonej produkcji.
Podsumowanie
Optymalizacja produkcji – jak wygląda proces? Wiemy już, że jest to bez wątpienia coś więcej niż jednorazowe działanie, to droga ciągłego dążenia do doskonałości operacyjnej. Wymaga kompleksowego podejścia – od analizy obecnego stanu, przez wdrażanie nowoczesnych narzędzi i technologii, po monitorowanie wydajności i zaangażowanie zespołu. Efektem jest firma produkcyjna działająca sprawniej, taniej i bardziej ekologicznie, co przekłada się na korzyści zarówno biznesowe, jak i społeczne. W dzisiejszym konkurencyjnym świecie zoptymalizowane procesy są nie tylko drogą do sukcesu, ale często warunkiem przetrwania na rynku.