How to Scientifically Choose Sandblasting Pressure? Core Parameter Analysis for Different Materials
In the mechanical processing industry, the success of sandblasting often hinges on the precise control of pressure parameters. Sandblasting pressure directly affects surface roughness, processing efficiency, and cost, while the sensitivity of different materials to pressure varies significantly. Below is a practical analysis of the selection logic to help you quickly determine the optimal parameters. I. Core Factors Influencing Sandblasting Pressure Material Hardness: Higher hardness materials (e.g., hardened steel, ceramics) require higher pressure (0.6-1.0 MPa) to remove surface oxidation layers; soft materials (e.g., aluminum, plastics) need lower pressure (0.2-0.4 MPa) to avoid deformation. Target Roughness: High pressure (≥0.8 MPa) can enhance surface adhesion, but excessive sandblasting may damage the substrate; precision parts recommend 0.3-0.5 MPa for micron-level control. Abrasive Type: Steel shots require 0.4-0.7 MPa, while brittle abrasives like glass beads or ceramic sand suggest 0.3-0.6 MPa to reduce fragmentation losses. II. Sandblasting Pressure Reference for Different Materials Aluminum/Magnesium Alloys: 0.2-0.35 MPa Low pressure combined with brown corundum or glass beads avoids micro-cracks caused by stress concentration while removing oxidation layers. Stainless Steel/Titanium Alloys: 0.5-0.8 MPa Medium-high pressure paired with silicon carbide abrasives effectively removes welding residues and controls Ra values between 3.2-6.3μm. Carbon Steel/Castings: 0.6-1.0 MPa High-pressure sandblasting efficiently removes rust but requires 60-80 mesh steel shots to prevent excessive equipment wear. Glass/Ceramics: 0.3-0.5 MPa Ultra-low pressure fine processing with aluminum oxide abrasives avoids edge chipping or hidden cracks. Plastics/Composites: 0.15-0.25 MPa Extremely low-pressure air sandblasting (recommended using walnut shells or plastic abrasives) for surface activation only. III. Key Verification Steps in Operation Step Pressure Testing: Use 0.1 MPa increments to sandblast different zones on a test piece, and observe surface morphology under a microscope to determine the critical damage threshold. Equipment Compatibility Calibration: Air compressor output stability (fluctuation 70%, install a dryer in the compressed air system to prevent abrasive clumping and pressure anomalies. Conclusion: Four Steps to Determine Optimal Parameters Material Diagnosis—Identify hardness, ductility, and surface defect types. Abrasive Matching—Abrasive hardness should be 1.5 times higher than the substrate. Initial Pressure Selection—Refer to industry benchmarks (e.g., ISO 8504-2). Dynamic Adjustment—Fine-tune by 0.05-0.1 MPa based on real-time surface inspection data. Through systematic pressure optimization, sandblasting efficiency can be improved by over 30%, while reducing rework rates and consumable costs. Regular process audits are recommended, and parameter effectiveness should be verified against standards like ASTM D968 or GB 8923. Click on the homepage to learn more about the solutions.
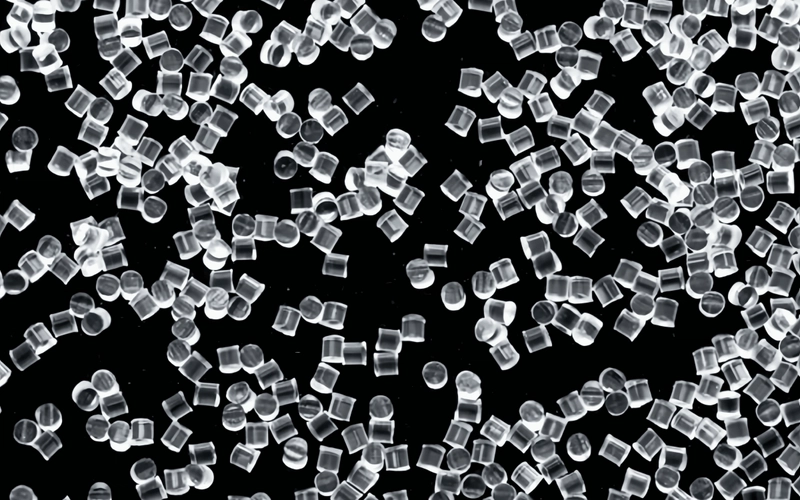
In the mechanical processing industry, the success of sandblasting often hinges on the precise control of pressure parameters. Sandblasting pressure directly affects surface roughness, processing efficiency, and cost, while the sensitivity of different materials to pressure varies significantly. Below is a practical analysis of the selection logic to help you quickly determine the optimal parameters.
I. Core Factors Influencing Sandblasting Pressure
Material Hardness: Higher hardness materials (e.g., hardened steel, ceramics) require higher pressure (0.6-1.0 MPa) to remove surface oxidation layers; soft materials (e.g., aluminum, plastics) need lower pressure (0.2-0.4 MPa) to avoid deformation.
Target Roughness: High pressure (≥0.8 MPa) can enhance surface adhesion, but excessive sandblasting may damage the substrate; precision parts recommend 0.3-0.5 MPa for micron-level control.
Abrasive Type: Steel shots require 0.4-0.7 MPa, while brittle abrasives like glass beads or ceramic sand suggest 0.3-0.6 MPa to reduce fragmentation losses.
II. Sandblasting Pressure Reference for Different Materials
Aluminum/Magnesium Alloys: 0.2-0.35 MPa
Low pressure combined with brown corundum or glass beads avoids micro-cracks caused by stress concentration while removing oxidation layers.
Stainless Steel/Titanium Alloys: 0.5-0.8 MPa
Medium-high pressure paired with silicon carbide abrasives effectively removes welding residues and controls Ra values between 3.2-6.3μm.
Carbon Steel/Castings: 0.6-1.0 MPa
High-pressure sandblasting efficiently removes rust but requires 60-80 mesh steel shots to prevent excessive equipment wear.
Glass/Ceramics: 0.3-0.5 MPa
Ultra-low pressure fine processing with aluminum oxide abrasives avoids edge chipping or hidden cracks.
Plastics/Composites: 0.15-0.25 MPa
Extremely low-pressure air sandblasting (recommended using walnut shells or plastic abrasives) for surface activation only.
III. Key Verification Steps in Operation
Step Pressure Testing: Use 0.1 MPa increments to sandblast different zones on a test piece, and observe surface morphology under a microscope to determine the critical damage threshold.
Equipment Compatibility Calibration: Air compressor output stability (fluctuation <5%) and nozzle wear (replace if aperture expands by 10%) directly affect pressure accuracy.
Environmental Variable Control: When humidity >70%, install a dryer in the compressed air system to prevent abrasive clumping and pressure anomalies.
Conclusion: Four Steps to Determine Optimal Parameters
Material Diagnosis—Identify hardness, ductility, and surface defect types.
Abrasive Matching—Abrasive hardness should be 1.5 times higher than the substrate.
Initial Pressure Selection—Refer to industry benchmarks (e.g., ISO 8504-2).
Dynamic Adjustment—Fine-tune by 0.05-0.1 MPa based on real-time surface inspection data.
Through systematic pressure optimization, sandblasting efficiency can be improved by over 30%, while reducing rework rates and consumable costs. Regular process audits are recommended, and parameter effectiveness should be verified against standards like ASTM D968 or GB 8923.
Click on the homepage to learn more about the solutions.